Walking around the old Holden factory site in Elizabeth, Paschal Somers points out each piece of machinery to explain what it does and how it could be brought back to life.
Though the massive factory complex in suburban Adelaide closed down three years ago, General Motors abandoned most of the machines to the site’s new owners when they sold the land, and they are still sitting there idle.
Rows of mechanical arms hanging from the ceiling were used to install the doors. Another row handled cockpit assembly. An arm used to install sunroofs is still in place. It cost $30,000 to build and $50,000 to develop, Somers says.
Across the complex, steel towers rise into the air, still able to lift a car body into the ceiling for transport elsewhere. Spare parts sit on old conveyer belts. An entire crane system is in perfect working order.
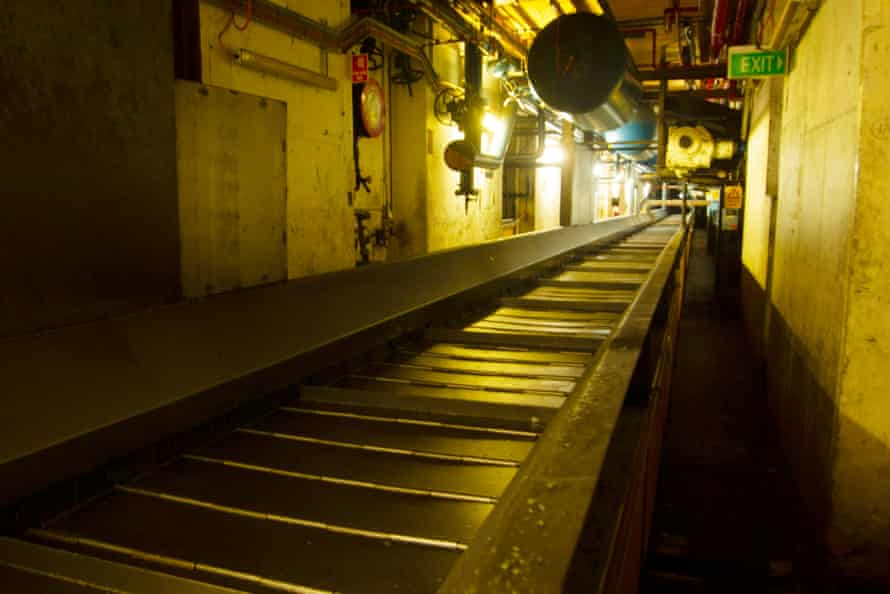
Over in the paint shop, the plant is in the same condition it was when it closed. Huge presses still stand in the press shop, even if they are in the process of being dismantled on account of their age.
“General Motors sold the factory to the new owners as is. Machines included,” Somers says. “All the bones are there. We could absolutely build electric cars here. It’s just a matter of retooling as you need.”
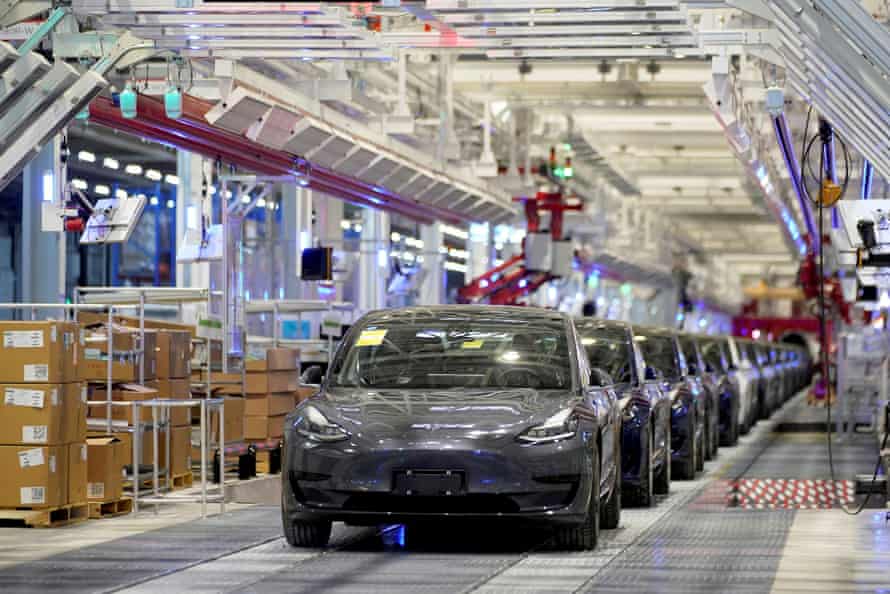
The 54-year-old site operations manager says that while some machinery has been sold off, the fixed infrastructure is still in place and it wouldn’t take much to install state-of-the-art hardware and bring it all back to life. He should know. Somers was one of seven former Holden workers who finished up on 17 October 2017, but stayed on with the new owners in what is now the Lionsgate business park.
“In the first couple of months after the closure it was it was tough,” Somers says. “I would take them through. People would come in, look around and say ‘it’s a nice shed’. It screamed at me inside. People didn’t see what we saw. No one seemed to understand what you could do with all this.
“If you were a start-up looking to move in, you’d be getting a six-to-18-month head start. Ask yourself, what’s the difference between an electric vehicle and a petrol vehicle? Not much, just the engine. You still need a wiring harness. You still need carpet. Sound dimmers. Glass. We could absolutely build electric vehicles – you just have to want to.”
That part – wanting to – is the perhaps the biggest hurdle in a nation whose political leadership has long thought of car manufacturing as hard work and electric vehicles a fad.
The situation is deeply frustrating to Electric Vehicle Council of Australia chief executive Behyad Jafari, who says he regularly talks to companies looking to manufacture EVs in Australia.
While critics charge that Australian labour costs are too high, Jafari says the actual work of manufacturing electric vehicles is half what it once was. Rather than “guys bending metal” it’s more about building the robots that build the cars – and with a highly educated workforce, Australia is highly competitive.
“On paper, Australia looks really good to these companies,” Jafari says.
“The second thing they ask is a question about the competitive landscape. What are governments doing? Essentially, they’re asking whether there will be a market for 50,000 vehicles in Australia – but we sell 7,000 electric vehicles a year here and there’s nothing in place to change that, when every other country in the world has an ambitious plan in place to change it.
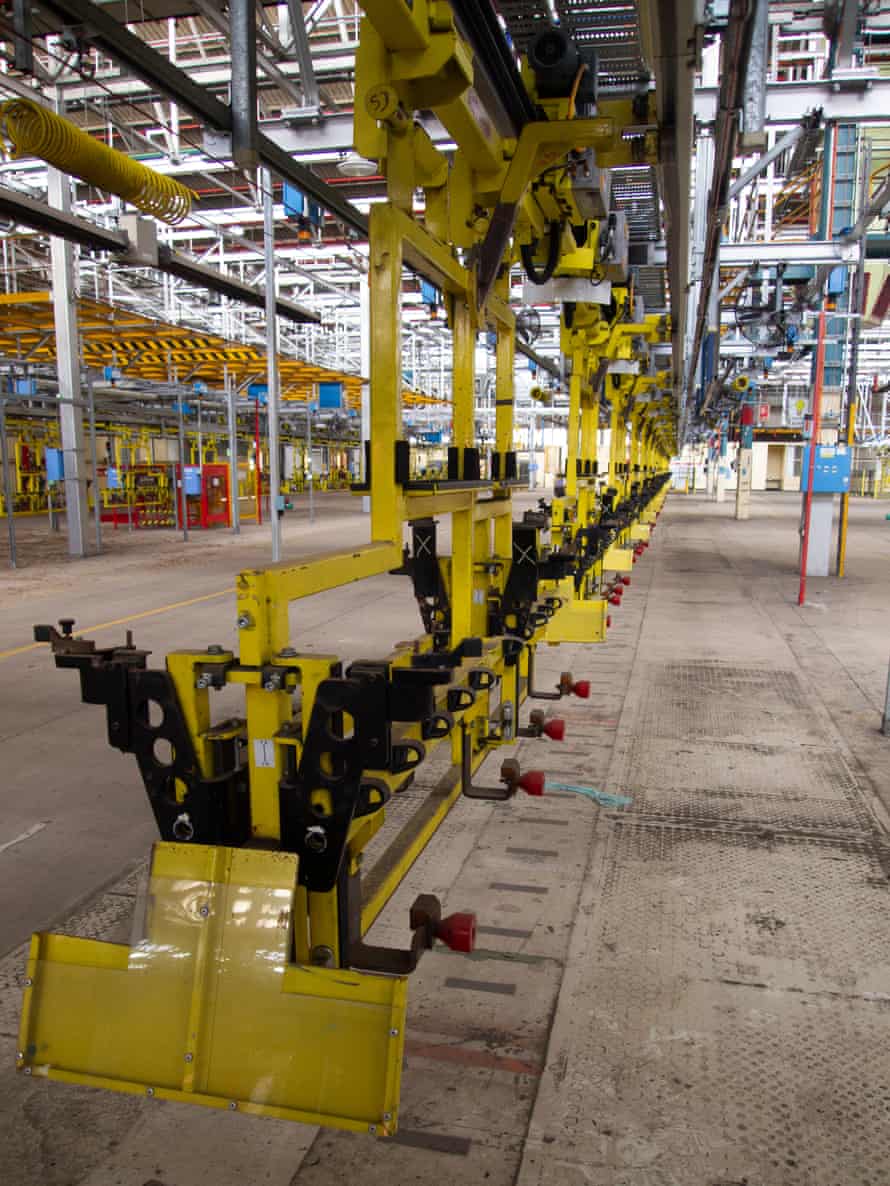
“It’s not even an accident anymore. It’s decided government policy that they should do nothing. They’ve entrenched that to the country as a whole, teaching us we can’t do these things. But the only reason we can’t do it is inaction.”
According to political economist Dr Mark Dean, that will have to change fast if Australia has any hope of achieving net zero emissions by 2050. A transition to electric would be required in a space of about 10 years – a feat that requires a plan.
“When you’ve mothballed the industrial-scale facilities that produce these things, you can’t just switch them back on,” Dean said. “And Elon Musk isn’t a genius who came up with the concept for EVs. His success is based on decades of public investment.
“There’s a lot of work needed to achieve decarbonisation and it’s work we can do. It would take a strong industry policy direction to identify something like this as a target, not a burden, and to whip up an economy geared to act on that. If we take risks, the rewards are enormous.”
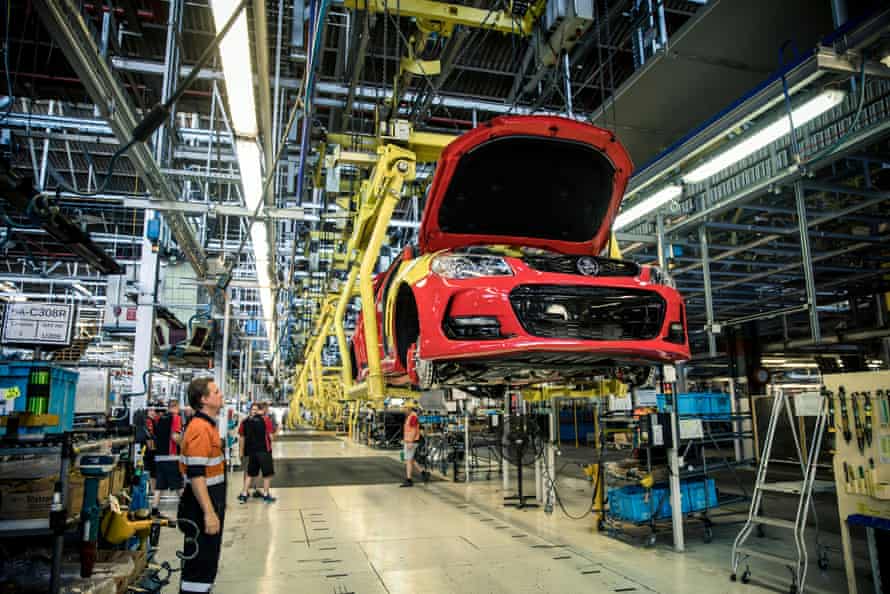
The vision for a new electric vehicle sector in Australia is not without its supporters.
Ed Husic, Labor’s shadow minister for industry and innovation, has been promoting the idea lately, saying on Tuesday that it represented an opportunity for Australia.
“I certainly accept it’s a massive challenge, right, to do this, especially after the government chased out car-makers from the country, but I think Australians do believe that we have got a great track record on manufacturing, we’ve got a lot to offer and why couldn’t we make a big difference, a big push in this space,” Husic said.
“With the 17 million cars we have on Australian roads, we need to upgrade the fleet so that we can see cars and transport in terms of reducing emissions is a big thing. So a win on manufacturing, a win of emissions. Why can’t we do it?”
Even on the local level there is support. In South Australia, SA Best parliamentarian Frank Pangallo says he will write to Elon Musk to invite the world’s richest man to set up an EV manufacturing plant in the state.
“Of course we can build electric cars here,” Pangallo said. “I’m no engineer, but I would say we already had the skills and expertise to build cars. We were building them for decades.
“The fact is that we know that we still have a great deal of infrastructure at the Holden site in Elizabeth. We know it’s still there. It’ll be a great opportunity for a start-up or a company like Tesla to move here and save considerably on set up costs. I’ll be impressing that upon Mr Musk.”
If Tesla has a powerful hold on the popular imagination, Australia has its own EV entrepreneurs.
Greg McGarvie is the founder of ACE Electric, an Australian start-up with plans to build electric utes, vans and passenger cars. While starting from scratch has taken more time, he says it has meant the company could rethink the best way to build a car and investigate the most advanced manufacturing techniques.
His vehicles are stitched together with a method similar to that used to build the Boeing Dreamliner, where sheets of carbon-fibre composite – a material two-to-three times stronger than steel – are chemically welded together.
The company has already recorded over $2 million in reservations, enough that they hope to begin production on the first 300 vehicles later this year.
While McGarvie says he’s had strong interest from south-east Asia and countries as far afield as eastern Europe, Australian authorities have been slow to act. It took the South Australian state government to offer development support at the end of 2020 for things to really get moving.
“We can manufacture these vehicles. Easy,” McGarvie says. “The only condition is government making it easy to proceed and to actually support it. The reason China is manufacturing 1.2 million electric vehicles a year is because their government said we will support anyone who’s got the go to set up auto.
“This is already happening everywhere else, Australia is just playing catching up. In five years, 10-years-time, if you’re parked at a traffic light and a fossil fuel smoker sitting beside you, it’ll be like going into a hospital or nursery and lighting a cigarette.”